Ohessa on lueteltuna joitakin oleellisimpia Materiakeskuksen tarjonnan tutkimusmenetelmiä.
Adheesiotestaus
Adheesiotestauksella määritetään pinnoitteen kiinnipysyvyys pohjamateriaalissa ja testiä käytetään mm. maalien sekä muiden pinnoitteiden testaukseen. Adheesiota voidaan testata monilla eri menetelmillä, esim. naarmutus- tai liimatappitestillä. Naarmutustestissä näytettä kuormitetaan kovalla timanttikärjellä ja liikutetaan samalla vaakatasossa, jolloin pinnalle muodostuu naarmu. Kasvattamalla timanttikärjen kuormitusta lineaarisesti testin aikana voidaan määrittää tarkat arvot pinnoitteen eri vauriomoodien kriittisille kuormille. Keskeisimmät tarkasteltavat vauriomoodit ovat koheesiovaurio (esim. pinnoitteen halkeilu) sekä adheesiovaurio (esim. pinnoitteen irtoaminen pohjamateriaalista) ja näiden tarkat kohdat voidaan määrittää esim. tutkimalla naarmua optisella mikroskoopilla tai pyyhkäisyelektronimikroskoopilla. Liimatappitestissä näytteen pintaan liimataan metallitappi muovituen tukemana ja liiman annetaan kovettua. Sen jälkeen muovituki poistetaan ja metallitappi vedetään irti näytteestä mekaanisella koestuslaitteella. Tapin irtoamiseen tarvittava voima jaettuna liimapaakun pinta-alalla kertoo pinnoitteen kestämän maksimikuormituksen. Testissä liimapaakku voi murtua myös ennen pinnoitteen irtoamista tai murtuma voi tapahtua pinnoite-liima-rajapinnalta, jolloin pinnoitteen maksimikuormitukselle saadaan määritettyä vain alaraja.
Laitteisto
- naarmutustestissä Lloyd LF Plus – hienomekaaninen aineenkoestuslaite ja omavalmisteinen näytteensiirtokelkka
- liimavetokokeessa Lloyd LF Plus – hienomekaaninen aineenkoestuslaite
- Pinnoitteen vaurioitumisen aiheuttavan kriittisen kuormituksen ja vauriomoodien määritys mikroskopialla
- standardit ASTM G171 (naarmutustesti) ja ASTM D4541 (liimatappitesti)
Näytevaatimukset
- näytteiden maksimimitat suuruusluokkaa 100×200 mm
- naarmutustestissä näyte ainakin yhteen suuntaan suora (tasainen tai sylinterimäinen suhteellisen suurella sylinterin halkaisijalla)
- liimatappitestissä tasainen näytepinta
Akkumateriaalitestaus
Laitteisto
- Elektrodien valmistaminen ja kennojen kokoaminen argon-hanskakaapissa.
- Galvanostaattiset tutkimukset (akkujen lataaminen ja purkaminen, kapasiteetin määritys).
- Syklinen voltammetria (sähkökemiallisten reaktioalueiden määritys).
- Sähkökemiallinen impedanssispektroskopia (akun komponenttien resistiivisyyden määritys).
- 2- tai 3-elektrodi -mittaukset.
Charpyn V-lovi iskukoe
Charpyn iskulujuuskokeella arvioidaan materiaalin iskunkestävyyttä. Kokeessa materiaalia lyödään tunnetulla energialla v-muotoisella vasaralla. Loven syvyydestä voidaan määrittää materiaalin iskunkestävyys ja sitkeys.
Laitteisto
- Charpyn iskuvasara
- Standardina SFS-EN ISO 148-1
Näytevaatimukset
Differentiaalinen pyyhkäisykalorimetria DSC
DSC-menetelmässä näytteeseen tuodaan lämpöenergiaa, ja sen lämpötilan muutosta seurataan. Mikäli näytteessä tapahtuu energiaa vieviä tai vapauttavia reaktioita, havaitaan tämä poikkeamana lämpötilan käyttäytymisessä. Mahdollisia havaittavia ilmiöitä ovat esimerkiksi
- Faasimuutokset; sulaminen, höyrystyminen jne.
- Kiteytyminen ja relaksaatiot
- Lasisiirtymät
- Kovettuminen (engl. curing)
Mittauksista voidaan selvittää muun muassa reaktiolämpötila, sekä kuinka paljon prosessi kuluttaa tai tuottaa energiaa.
Laitteisto
- TAinstruments: Discovery DSC
- Lämpötilaväli -100° C:sta +725° C:een.
- Automaattinen näytteenvaihtaja 50:lle näytteelle.
Näytevaatimukset
- Tyypillinen näytemäärä 5-20 mg
- Soveltuu pienikokoisille ja jauhemaisille näytteille. Näytepidin halkaisijaltaan 6 mm, tilavuus max. 40 μl
Dynaaminen aineenkoestus
Dynaamisessa aineenkoestuksessa testataan materiaalin mekaanista kestävyyttä esim. veto-, puristus-, taivutus- tai vääntökuormituksessa muuttamalla materiaalin kuormitusta ja muodonmuutosta kontrolloidusti. Analyysin tuloksena saadaan määritettyä vastaavia materiaalin lujuusteknisiä ominaisuuksia kuten esim. vetolujuus, puristuslujuus, taivutuslujuus tai vääntölujuus. Vetokokeessa näyte kiinnitetään lujasti molemmista päistään ja vedetään tiettyyn kuormitukseen/venymään tai murtumaan saakka. Puristustestissä näytettä puristetaan kahden levyn tai sylinterin välissä tiettyyn kuormitukseen/puristumaan tai murtumaan saakka. Taivutustestissä näyte asetetaan kahden tuen päälle ja kuormitus tapahtuu joko yhdestä (3-pistetesti) tai kahdesta pisteestä (4-pistetesti). Näytettä kuormitetaan tiettyyn kuormitukseen/taipumaan tai murtumaan saakka. Vääntötestissä näyte kiinnitetään lujasti molemmista päistään ja väännetään tiettyyn kuormitukseen/vääntymään tai murtumaan saakka. Testaus voidaan toteuttaa myös syklisesti vaihtuvalla kuormituksella, jolloin saadaan selville materiaalin väsymiskestävyys, tai eri testityyppejä voi yhdistää, esim. yhdistetty veto- ja vääntötesti. Mekaaniselle testaukselle on olemassa lukuisia standardoituja mittausmenetelmiä, joissa määritellään mittauksen suorittamisen lisäksi myös standardinäytteen koko ja muoto.
Laitteisto
- Instron 8874
- dynaaminen, 2-akselinen koestuslaite
- kapasiteetti 1 N – 25 kN, maksimivääntömomentti 100 Nm
- kuormitustaajuus < 30 Hz
- materiaalin veto-, puristus-, taivutus-, kierto- tai väsymiskokeet eri standardien mukaisesti
- olosuhdekammio testaukseen eri lämpötiloissa
Näytevaatimukset
- vetokokeessa kiinnitysleukojen maksimiavautuma (=näytteen maksimipaksuus) n. 10 mm
- käytetty standardi määrittelee useimmiten näytteen mitat ja muodon, näistä poikkeavat näytekoot tarkasteltava tapauskohtaisesti laitteen kapasiteetti huomioiden
- koestuslaitteen vapaa korkeus (esim. näytteen pituus vetokokeessa/näytteen korkeus puristuskokeessa) maksimissaan n. 400-500 mm
Dynaaminen valonsironta ja Zeta-potentiaali
Dynaaminen valonsironta (engl. DLS, Dynamic Light Scattering) on menetelmä nanopartikkelien kokojakauman ja Zeta-potentiaalin määritykseen. Menetelmässä partikkelit sekoitetaan nesteeseen ja seos annostellaan kyvettiin. Kyvetti ladataan mittalaitteeseen, jossa näytteeseen kohdistetaan laservaloa. Brownin liike saa partikkelit liikkumaan nesteessä, joka aiheuttaa muutoksia laservalon sirontakuvioon. Koska Brownin liike on riippuvainen partikkelikoosta, voidaan näistä sirontakuvion muutoksista laskea partikkelien kokojakauma.
Zeta-potentiaali on partikkelin pintavarausten summa partikkelin ja liuottimen välissä. Zeta-potentiaalia hyödynnetään yleisesti dispersioiden kolloidisen stabiiliuden määrityksessä: suuret negatiiviset tai positiiviset arvot kertovat dispersion stabiiliudesta ja pienillä arvoilla partikkelit agglomeroituvat helpommin. Zeta-potentiaalia määritettäessä partikkelit ladataan erikoiskyvettiin jolla saadaan aikaiseksi sähkökenttä nesteeseen. Vastaavalla tavalla sähkökentän aiheuttamista muutoksista sirontakuvioon voidaan laskea Zeta-potentiaalin arvo.
Laitteisto
- Malvern Zetasizer Nano ZS mittalaite DLS-määrityksiin
Näytevaatimukset
- Partikkelikoko Zeta-potentiaalin määritykseen 3,8 nm -> 100 µm
- Partikkelikoko 0,3 nm -> 10 µm
Dynaaminen väsytyskoe

Väsyttävään materiaali- ja rakennetutkimukseen tarkoitettu kuormituskehä on Sveitsiläisen Walter+Bai ag:n toimittama ratkaisu, jonka suurin kuormitusvoima on 500 kN. Tällä kuormituksella voidaan tehdä sekä dynaamisia että staattisia testejä. Laitteiston testausohjelmistolla voidaan tehdä vakiotestien lisäksi myös räätälöityjä testaussarjoja. Venymän ja puristuman mittaukseen laitteeseen on kytkettävissä sekä mekaaninen että videoekstensiometri. Lisäksi laitteistoon voidaan liittää olosuhdekammio, joka mahdollistaa pienten testikappaleiden koestustutkimukset kylmissä ja kuumissa oloissa.

Teknisiä tietoja
Suurin testausvoima (staat./dyn.): 500 kN
Suurimman testikappaleen koko: 6000 mm x 1200 mm x 1800 mm (P x L x K)
Suurin dynaaminen testausamplitudi: +/- 200 mm
Siirtymäresoluutio: < 0.001 mm
Siirtymätarkkuus: +/- 0.5 %
Suurin sylinterin männän nopeus: 2 m/s
Rungon jäykkyys: 1200 kN/mm
Tasaiset kappaleet: paksuus 0-21 mm ja 20-41 mm, tartunta-ala 85 x 100 mm
Sylinterikappaleet: halkaisija 5-12 mm ja 10-21 mm, tartunta korkeus 85 mm
Olosuhdekammion teknisiä tietoja
Lämpötila-alue: -100 – +600 °C
Sisämitat: 350 mm x 300 mm x 550 mm (S x L x K).
Dynaaminen testaus, taajuusominaisuuksia:

FTIR-spektrometrit
Infrapunaspektrometrialla voidaan tutkia näytteen kemiallista rakennetta. Menetelmässä lämpösäteily saa molekyylit ja niiden väliset sidokset värähtelemään. Mittaustuloksena saadaan ns. absorptiospektri, josta voidaan lukea erilaisille kemiallisille rakenneosille tyypillisiä värähdyksiä ja tunnistaa ne niiden perusteella. Käytetään mm. aineen tunnistamiseen muiden menetelmien rinnalla. FTIR tulee sanoista Fourier Transform[TS1] Infrared Spectroscopy.
Laitteisto
- Thermo Nicolet iS50
- Mittausalue 4000–400 cm-1
- Ohjelmistosta löytyy laaja spektrikirjasto spektrien tulkinnan avuksi
- Laitteeseen on saatavilla monipuolisesti detektoreita ja objektiiveja erityyppisille näytteille:
- Matalan tulokulman objektiivi ohutkalvoille
- Transmissiodetektori kalvojen, nesteiden, jauheiden ja kaasujen mittaukseen
- Multi-sampler suurien näytesarjojen mittaamiseen
- Erilaisia ATR-kiteitä nopeaan jauheiden, nesteiden ja kalvojen mittaukseen
- Agilent Cary 620/670
- Kuvantava infrapunaspektrometri
- Mittausalue 3850–750 cm-1 FPA-detektorilla[TS2]
- Pistemittaus tai kartta
- Karttamittauksessa 128 x 128 pikselin FPA-detektori
- 5,5 x 5,5 µm tai 1,1 x 1,1 µm pikselikoko
- Mittaus tyypillisesti läpäisymoodissa
- Soveltuu myös valoa läpäisemättömille näytteille heijastusmoodissa
- [TS3] Soveltuu erityisesti orgaanisille aineille
Näytevaatimukset
- Vedetön
Hienomekaaninen aineenkoestus
Hienomekaanisessa aineenkoestuksessa testataan materiaalin mekaanista kestävyyttä esim. veto-, puristus- tai taivutuskuormituksessa muuttamalla materiaalin kuormitusta ja muodonmuutosta kontrolloidusti. Analyysin tuloksena saadaan määritettyä vastaavia materiaalin lujuusteknisiä ominaisuuksia kuten esim. vetolujuus, puristuslujuus tai taivutuslujuus. Vetokokeessa näyte kiinnitetään lujasti molemmista päistään ja vedetään tiettyyn kuormitukseen/venymään tai murtumaan saakka. Puristustestissä näytettä puristetaan kahden levyn tai sylinterin välissä tiettyyn kuormitukseen/puristumaan tai murtumaan saakka. Taivutustestissä näyte asetetaan kahden tuen päälle ja kuormitus tapahtuu joko yhdestä (3-pistetesti) tai kahdesta pisteestä (4-pistetesti). Näytettä kuormitetaan tiettyyn kuormitukseen/taipumaan tai murtumaan saakka. Mekaaniselle testaukselle on olemassa lukuisia standardoituja mittausmenetelmiä, joissa määritellään mittauksen suorittamisen lisäksi myös standardinäytteen koko ja muoto.
Laitteisto
- Lloyd LF Plus
- 1-akselinen koestuslaite
- kapasiteetti 0.01 N – 1 kN
- materiaalin veto-, puristus- ja taivutuskokeet eri standardien mukaisesti
Näytevaatimukset
- vetokokeessa kiinnitysleukojen maksimiavautuma (=näytteen maksimipaksuus) n. 8 mm
- käytetty standardi määrittelee useimmiten näytteen mitat ja muodon, näistä poikkeavat näytekoot tarkasteltava tapauskohtaisesti laitteen kapasiteetti huomioiden
- koestuslaitteen vapaa korkeus (esim. näytteen pituus vetokokeessa/näytteen korkeus puristuskokeessa) maksimissaan n. 300-400 mm
Jauheröntgendiffraktio XRD
Röntgendiffraktio (engl. X-Ray diffraction) on menetelmä, jolla tutkitaan materiaalin kiderakennetta. Röntgendiffraktio on yksi materiaalitutkimuksen perustyökaluista ja se soveltuu materiaalien karakterisointiin, tunnistukseen sekä uusien materiaalien rakenteen tutkimukseen. Jauheröntgendiffraktiolla viitataan diffraktioon monikiteisestä materiaalista, kuten esimerkiksi jauheesta tai metallista.
Menetelmä perustuu röntgensäteiden sirontaan kiteisen materiaalin atomeista. Kun materiaali on kiteinen, ts. sen atomirakenne on säännöllinen, siitä sironneet röntgensäteet muodostavat interferenssin seurauksena diffraktiokuvion (diffraktogrammin), joka on aina kullekin kiderakenteelle yksilöllinen. Röntgendiffraktiolla voidaan selvittää monia aineen ominaisuuksia, kuten esimerkiksi
- Näytteen sisältämät faasit
- Faasien suhteelliset massaosuudet (ts. kvantitatiivinen analyysi)
- Faasien kidekoot
- Kidesuunnat
- Jäännösjännitykset
- Lämpötilan funktiona tapahtuvat faasitransitiot
- Lämpölaajenemiskerroin
- Amorfisuusaste
Lisäksi analyysit voidaan suorittaa säteilyn tulokulmaa säätämällä kvalitatiivisesti syvyyden funktiona, esimerkiksi pinnoitteesta.
Laitteisto
- Bruker D8 DISCOVER
- Eulerin kehto
- Näytteen kierrot kahden akselin suhteen ja X-Y-Z –siirrot mahdollisia
- Kaikki akselit motorisoituja ja mahdollista käyttää näytteen asettamisessa ja mittauksessa
- Bulkki- ja jauhenäytteille, ohutkalvoille ja –levyille
- Näytteen maksimikorkeus 40 mm ja maksimipaino 1 kg
- Kehto mahdollistaa mm. tekstuurimääritykset (kiteiden suuntautuminen), jäännösjännitysten määrittämisen, reflektometrimääritykset (XRR) ohutkalvojen mittaamiseksi, faasien syvyysprofiloinnin (GID) kerroksellisilla näytteillä sekä mittaukset kuoppalevyistä tarkasti fokusoidun röntgensäteilyn avulla (mikrodiffraktio ja high throughput screening)
- Kapillaarispinneri
- Mittaukset kapillaareissa
- Kapillaarin pyöritys mahdollista mittauksen aikana
- Jauhenäytteille, nestemäisille näytteille, suspensioille
- Voidaan käyttää, kun näytemäärät ovat pieniä
- Käytetään parinjakaumafunktioanalyysin (PDF) tekemiseen, kun halutaan tutkia nanokiteisten tai amorfisten materiaalien lähijärjestystä.
- Mahdollista käyttää pienkulmasirontamäärityksissä (SAXS) kolloidinäytteille
- Anton Paar DCS 350 –olosuhdekammio
- Diffraktiomittaukset matalissa ja korotetuissa lämpötiloissa in situ
- Ilmassa/inertissä kaasussa huoneenlämmöstä +350 °C:een
- Vakuumissa -100 °C: sta +350 °C:een
- Näytteen maksimihalkaisija 25 mm
- Asennetaan Eulerin kehtoon, jolloin näytteelle voidaan tehdä mm. tekstuurimääritys halutussa lämpötilassa tai seurata faasitransitiota lämpötilan funktiona
- LynxEye-detektori
- 1D –detektori, 192 kanavaa
- Mahdollista käyttää Cr-, Co-, Cu- ja Mo-säteilyn kanssa
- Fluoresenssisäteilyn rajoittaminen elektronisesti signaalikohina –suhteen parantamiseksi rauta- tai kobolttipitoisilla näytteillä Cu-säteilyä käytettäessä. Vaihtoehtoisesti voidaan käyttää Mo-säteilyä.
- Mittaukset normaalia Bragg-Brentano –geometriaa käyttäen tai parallel beam –geometrialla (Göbelin peili). Mahdollistaa myös epätasaisten näytteiden mittaamisen.
- Käytettävissä Cu-säteily (Kα1 0,1540562 nm) ja Mo-säteily (Kα1 0,070930 nm)
- Monipuoliset mittaus- ja analyysiohjelmistot, joihin sisältyy mm. Rietveld-laskenta
- Direktiivien 2006/42/EC, 2006/95/EC ja 2004/108/EC mukainen
- Mitattu säteilyannos mittausolosuhteissa: 133 nSv/h (Mo, 50 kV/60 mA)
Näytevaatimukset
- Jauhenäytettä vähintään 1,5 ml standardinäytepitimeen. Pienemmällä näytemäärällä mittaukset ovat aikaa vieviä ja epätarkempia.
- Näytteen maksimikorkeus 40 mm ja maksimipaino 1 kg
- Mitattava kohde oltava yli 0,3 mm (pienin spottikoko)
Lujuustutkimus
Lujuustutkimuksessa selvitetään kappaleen lujuus staattisilla tai dynaamisilla vetokokeilla. Yleisin rakenteiden rasitusmuoto on staattista eli pysyvää kuormitusta. Näissä tilanteissa rakenteiden jännitykset ei saa ylittää myötölujuutta. Tätä myötörajaa voidaan pitää lujuuslaskujen lähtökohtana, sillä jännitykset jäävät kimmoalueelle ja venymät palautuvat jännityksen poistuttua. Vetokoneella tehtävällä aineenkoetuksella saadaan mitattua materiaalin lujuusominaisuudet, josta piirretään jännitys-venymäkäyrä ja josta voidaan erottaa kimmoalue, tasavenymäalue ja kurouma-alue.
Muita lujuusominaisuuksia (dynaamisia), joita materiaaleista tutkitaan ovat vaihtelevan kuormituksen alaisena olevat kappaleet ja rakenteet, jolloin tutkitaan väsymislujuutta. Väsymislujuus on aina pienempi kuin myötölujuus. Iskumaisissa kuormitustapauksissa tärkeä tieto on materiaalin iskusitkeys, jota tutkitaan iskuvasaralla esimerkiksi Charpyn iskuvasaratestillä.
Muodonmuutoskykyyn vaikuttavat:
- lämpötilan laskiessa iskusitkeys pienenee.
- kuormitusnopeus: kuormitusnopeuden kasvaessa lujuus kasvaa
- lämpötilasta: lämpötilan noustessa lujuus pienenee
- mikrorakenne
- voimakkaat jännityskeskittymät edistävät sitkeyden pienenemistä
- iskusitkeyteen vaikuttaa iskumaisen kuormituksen nopeus
Kaasuadsorptio BET&BJH
BET (Brunauer-Emmett-Teller) -kaasuadsorptio menetelmää käytetään huokoisten ja nanokokoisten materiaalien ominaispinta-alan määritykseen. BJH (Barrett-Joyner-Halenda) -menetelmällä on mahdollista määrittää näiden huokoskoko ja –tilavuus. Menetelmät perustuvat kaasumolekyylien adsorptioon materiaalin pintaan.
Laitteisto
- Micromeritics Tristar II
- Adsorbaattina typpi tai hiilidioksidi
- Määritettävissä oleva ominaispinta-ala > 0,01 m2/g
- Määritettävissä oleva kokonaispinta-ala > 0,1 m2/g
- Määritettävissä oleva huokostilavuus > 4 × 10-6 cm³/g
Näytevaatimukset
- Huokoisuuteen liittyvät määritykset pääasiallisesti vain mesohuokoisille materiaaleille (huokoskoko 2-50 nm). Ominaispinta-alamäärityksille ei huokoskokorajoitteita.
- Näytteen oltava kuiva, joko jauhemainen tai kiinteä kappale.
- Kiinteän kappaleen tapauksessa maksimidimensiot 2,8 mm/2,8 mm/2,8 mm (p/l/k)
- Tyypillinen näytemäärä kuivana n. 0,1 – 1 g. Riippuu kuitenkin näytteestä: korkean ominaispinta-alan omaavaa materiaalia tarvitaan vähemmän, vähemmän pinta-alaa omaavaa näytettä enemmän.
Korroosiopotentiaali
Sähkökemiallista korroosiopotentiaalimittausta käytetään metalliesineiden korroosio-ominaisuuksien, kuten korroosioalttiuden ja -nopeuden, passivoitumistaipumuksen sekä pinnoitteen laadun, tutkimiseen. Menetelmä soveltuu erityisen hyvin vertailevaan tutkimukseen, jossa selvitetään eri materiaalien korroosiokäyttäytymistä tietyssä ympäristössä tai yksittäisen materiaalin käyttäytymistä eri korroosioympäristöissä. Testin avulla saadaan suuntaa antavaa tietoa pinnoitteen korroosio-ominaisuuksista muutamissa tunneissa eli huomattavasti perinteistä suolasumukoetta nopeammin.
Mittauksessa tutkittava kappale altistetaan korrosoivalle nesteelle (esim. suolaliuos) ja näytteen potentiaali sekä sen läpi kulkevaa virta määritetään potentiostaatilla 3-elektrodikytkentää käyttäen. Mittaus voidaan toteuttaa joko staattisesti vakiovirralla tai dynaamisesti, jolloin potentiaalia muutetaan hallitusti ja mitataan virtaa (tai päinvastoin). Lisäksi voidaan suorittaa ilman virransyöttöä tapahtuva lepopotentiaalimittaus, jonka avulla saadaan tietoa mm. pinnan stabiiliudesta, pinnoitteen tiiveydestä ja oksidikerroksen muodostumisesta.
Laitteisto
Näytevaatimukset
Korroosiotestaus
Metallisten materiaalien kestoa pinnoitettuna tai pinnoittamattomana voidaan testata keinotekoisissa olosuhteissa suolasumukokeiden avulla. Testi simuloi korroosioympäristöä suolasumutuksella ja korroosionopeus kasvaa verrattuna luonnolliseen ympäristöön. Altistusta voidaan tehdä tunneista useisiin satoihin. Suolasumukokeet sopivat usein korroosiokokeiksi, kun halutaan analysoida nopeasti orgaanisten ja epäorgaanisten pinnoitteiden epäjatkuvuuskohtia, huokosia tai vaurioita.
Laitteisto
- SFS – EN ISO 9227 (Neutraali suolasumukoe NSS 5 % suolaliuos)
- Testikappaleiden kuvaus ennen ja jälkeen testin.
Näytevaatimukset
Kovuustestaus
Kovuusmittaus on nopea ja yksinkertainen tapa määrittää materiaali ominaisuuksia. Kovuus on materiaalin kyky vastustaa siihen tunkeutuvaa esinettä, naarmuuntumista, kulumista tai leikkautumista. Yksinkertaisimmillaan kovuuden määritys voidaan toteuttaa hankaamalla materiaaleja toisiaan vasten ja verrata niiden kykyä naarmuttaa toisiaan. Materiaalin kovuus ei ole sinänsä materiaaliominaisuus, vaan se on riippuvainen monista tekijöistä kuten vetomurtolujuudesta, murto- ja iskusitkeydestä sekä kimmoisista ominaisuuksista. Kovuuden mittauksen helppouden, nopeuden ja toistettavuuden vuoksi, tämä on erinomainen materiaaliominaisuuksien testausmenetelmä. Kovuuden standardisoituja mittausmenetelmiä on useita ja soveltuvimman menetelmän valintaan vaikuttaa paljolti tutkittava materiaali. Näitä standardisoituja mittausmenetelmiä ovat tyypillisesti käytettävät Rockwellin, Vickersin ja Brinellin kovuuskokeet eri variaatioineen.
Laitteisto
- Affri 206 RSD
- Semiautomaattinen
- 0,5 % tarkkuus
- SFS-EN ISO 6508-1 ja ASTM E18 mukaiset Rockwellin kovuusmittaukset.
- Näytteen maksimikorkeus 215 mm
- Käytettävissä oleva voimaväli: 588.4 N – 980.7 N – 1471 N (60 kgf – 100 kgf – 150 kgf)
- Rockwell-kovuustestit: HRC – HRA – HRD – HRB – HRF – HRG – HRL – HRM – HRR
- Durascan-20 G5 kovuusmittari
- Vickers- ja Knoop-kovuustesteihin
- EN ISO 6507, ASTM E384 ja JIS Z 2251 mukaiset Vickers-kovuusmittaukset.
- EN ISO 4545, ASTM E384 sekä JIS Z 2251 mukaiset Knoop-kovuusmittaukset.
- Näytteen maksimikorkeus 260 mm.
- Käytettävissä oleva voimaväli: 0.098 N – 612.9 N (10 gf – 62.5 kgf)
- Matsuzawa MMT-X7
- Mikrokovuusmittari Vickers-kovuuksien määrittämiseen on hyödyllinen pienten kohteitten tutkimuksessa.
- SFS-EN ISO 4516 mukainen Vickers-kovuusmittaus
- Näytteen maksimikorkeus 120 mm.
- Käytettävissä oleva voimaväli: 49.03 mN – 9807 mN (5 gf – 1000 gf)
- Ernst AT130D
- Rockwell-, Vickers- sekä Brinell-kovuuskokeet.
- SFS-EN ISO 6506-1 mukainen Brinell-kovuusmittaus
- SFS-EN ISO 6507-1 mukainen Vickers-kovuusmittaus
- SFS-EN ISO 6508-1 mukainen Rockwell-kovuusmittaus
Näytevaatimukset
Kovuusmittaus
Kovuuden määritelmänä pidetään yleensä materiaalin kykyä vastustaa siihen tunkeutuvaa esinettä, naarmuuntumista, kulumista tai leikkaamista. Yksinkertaisimmillaan kovuuden määritys voidaan toteuttaa hankaamalla materiaaleja toisiaan vasten ja verrata niiden kykyä naarmuttaa toisiaan, kuten Mohsin menetelmässä tehdään.
Materiaalin kovuus ei ole sinänsä materiaaliominaisuus, vaan se on riippuvainen monista tekijöistä kuten vetomurtolujuudesta, murto- ja iskusitkeydestä sekä kimmoisista ominaisuuksista. Kovuuden mittauksen helppouden, nopeuden ja toistettavuuden vuoksi, tämä on erinomainen materiaaliominaisuuksien testausmenetelmä. Kovuuden standardisoituja mittausmenetelmiä on useita ja soveltuvimman menetelmän valintaan vaikuttaa paljolti tutkittava materiaali. Näitä standardisoituja mittausmenetelmiä ovat tyypillisesti käytettävät Rockwellin, Vickersin ja Brinellin kovuuskokeet eri variaatioineen.
Lisätietoa käytössä olevasta laitteistosta löydät täältä.
Rockwell-kovuus (SFS-EN ISO 6508–1)
Rockwellin kovuusmittausmenetelmässä painimen tunkeuman syvyys määritetään tietyssä mielivaltaisessa testaus-olosuhteessa, jossa sovitun kokoinen ja muotoinen sekä tiettyä materiaalia oleva paininkärki painetaan koekappaleen pintaan kahdessa vaiheessa kuvan mukaisella tavalla. Kovuusalue (A, B, C, etc.) määräytyy painimen ja testikuorman mukaan.

Rockwellin kovuus- ja pintakovuuskokeissa käytetään kovuuden määrittämiseksi timanttikartio- tai kovametallikuulapaininkärkeä. Kovametallipaininkärkeä pidetään yleisesti Rockwellin kokeessa vakiopaininkärkenä. Teräskuulapaininkärkeäkin voidaan käyttää, mikäli tuotespesifikaatioissa on näin määritelty tai mikäli siitä on erikseen sovittu. Tässä on kuitenkin huomioitava, että kovametallikuulalla saadut tulokset saattavat poiketa merkittävästikin teräskuulalla saaduista tuloksista.
Kovuusarvot esitetään A, B, C, D, E, F, G, H, K, N, T alueilla. Mitä suurempi lukuarvo eri alueissa on, sitä kovempaa materiaali on. Asteikot N ja T ovat ns. Rockwellin pintakovuuskokeita.
Katso tiedot Materia tutkimuskeskuksen käyttämistä kovuusmittareista täältä.
Vickers-kovuus (SFS-EN ISO 6507–1)
Vickersin menetelmä on usein helpompi käyttää kuin muut kovuuden mittaustavat, sillä tässä vaaditut laskentamenetelmät ovat riippumattomia painimen koosta ja toisaalta samaa paininta voidaan käyttää kaikille materiaaleille kovuudesta riippumatta.
Vickersin menetelmässä materiaalin kovuus määritetään laitteistolla, jossa neliöpohjainen säännöllinen timanttipyramidi painetaan koekappaleeseen koevoimalla F. Koevoiman poistamisen jälkeen mitataan koekappaleen pintaan jääneen painauman lävistäjät d1 ja d2. Vickersin kovuus HV lasketaan yhtälöstä

missä F on koevoima ja d on lävistäjien d1 ja d2 aritmeettinen keskiarvo.
Painuman oletetaan olevan neliöpohjaisen säännöllisen pyramidin muotoinen ja sen kärkikulma on sama kuin paininkärjellä.

Vickersin kovuuden arvo esitetään muodossa xxxHVyy, kuten esimerkiksi 440HV30. Tällöin
- 440 on kovuuden arvo,
- HV on Vickersin kovuuden tunnus,
- 30 on koevoiman likimääräinen suuruus kilogrammavoimana (kgf), missä 30 kgf = 294,2 N,
- Lisäksi ilmoitetaan kuormitusaika, silloin kun se poikkeaa määritellystä ajasta (10 – 15s).
Brinell-kovuus (SFS-EN ISO 6506–1)
Brinellin kovuuskokeen kehitti ruotsalainen tohtori Johan August Brinell vuonna 1900, joka oli ensimmäinen laajasti käytetty ja standardisoitu kovuuden mittausmenetelmä tekniikassa ja metallurgiassa. Tästä hyvänä esimerkkinä ovat kulutusteräkset, jotka ovat nimensä mukaisesti teräksiä, joilla on hyvä ja tavanomaisia rakenneteräksiä huomattavasti parempi kulumiskestävyys missä tärkeänä ominaisuutena on teräksen pinnan kovuus. Kulutusterästen nimessä olevalla luvulla ilmoitetaan kovuus Brinelleinä esim. Hardox 400.
Brinellin kovuudenmittauksessa mitataan kovametallipallon painaumaa tutkittavaan materiaalin staattisen kuormituksen alaisena mittausajan ollessa vakio. Standardissa ISO 6506 Määritellään vain kovametallipaininkärjen käyttö, jonka tunnus on HBW ja sitä ei tulisi sekoittaa aikaisempiin tunnuksiin HB tai HBS, joita käytettiin teräskuulapaininkärjillä.
Mittauksessa käytetään tavallisesti 10, 5, 2.5 tai 1 mm:n halkaisijaa olevaa kiilloitettua kovametallipalloa painimena, jossa mittausvoimat ovat 1 kgf:n ja 3000 kgf:n väliltä.
Koe suoritetaan niin, että paininkärki (kovametallikuula, halkaisija D) painetaan koekappaleen pintaan. Painuman halkaisija d mitataan koevoiman F poistamisen jälkeen.
Brinellin kovuus on voiman ja kuulan aiheuttaman painumakalotin pinta-alan lukuarvojen suhde. Painuman oletetaan säilyttävän kuulan muodon ja sen pinta-ala lasketaan painuman halkaisijoiden keskiarvosta ja kuulan halkaisijasta.


Läpäisyelektronimikroskopia, TEM
TEM on erittäin suuren erotuskyvyn omaava mikroskooppi, joka vaatii usein kouluttautuneen erikoislaboratoriohenkilöstön perusteellisen näytteenvalmistusprotokollan. Jos näyte on nanokokoluokan hiukkanen, ns. nanopartikkeli, on TEM useimmiten ainoa kuvausmenetelmä, jolla hiukkanen voidaan nähdä. TEM:lla kuvattaessa näyte läpivalaistaan elektronisuihkulla, jolloin näytteeltä vaaditaan, että korkeaenergisen elektronin on päästävä siitä läpi. Toisaalta luonteensa puolesta kohteesta voidaan myös muodostaa 3D-tomografeja eli kolmeulotteisia kuvia kääntämällä kuvattavaa kohdetta, jolloin se projisoidaan eri suunnista. Näistä projektioista voidaan matemaattisin menetelmin rekonstruoida kohteen 3D-rakenne.
Laitteisto
- JEM-2100F (JEOL Co, Tokyo, Japan)
- Kiihdytysjännite: 200kV (kenttäemissiotykki, Schottky type)
- Käytettävät suurennokset: 50–1 500 000 X (läpäisymoodi)
- Resoluutio: ~ 0.1 nm
- Muuta: Pyyhkäisy-läpäisy-moodi (Scanning-transmission)
- Digitaalinen kamera: Quemesa 11 MPix CCD (Olympus-SIS, Münster, Germany)
- Alkuainenalysaattori (EDS): Nestetyppijäähdytteinen Thermo Noran 7 EDS detektori (ThermoFisher Scientific, Madison, WI, USA)
- Näytteenpitimet: rutiini (yhden näytteen), moninäytepidin (kolme näytettä), High Tilt-pidin tomografiaan (yhden näytteen).
Näytevaatimukset
- Ei haihtuvia komponentteja
Luonnonkuitukomposiittien valmistuksesta, testauksista ja tutkimuksesta
Luonnonkuitukomposiiteissa yhdistyvät luonnonkuitujen ja muovimatriisin parhaat ominaisuudet. Luonnonkuitukomposiittien etuja ovat mm. ympäristöystävällisyys, kierrätettävyys, helppo muotoiltavuus, valmistuksen kustannustehokkuus, kuitujen suuri vetolujuus ja muut mekaaniset ominaisuudet.
Luonnonkuitukomposiitteja varten valmistettiin hampusta pitkäkuituja erilaisilla käsittelyillä kotimaassa kasvatetuista kuituhamppukasveista (mekaaninen käsittely, alkalikäsittely, entsymaattinen liotus, höyrykäsittely ja puutislekäsittely). Kuitujen mekaaniset ominaisuudet testattiin Lloyd-vetotestauslaitteella ja karakterisoitiin optisella mikroskoopilla, elektronimikrospoopilla ja FTIR:llä sekä kosteuden imeytymiskäyttäytymistä testattiin punnitusmenetelmällä. Kuiduista valmistettiin myös laminoimalla komposiittilevyjä, joissa oli lujitteena noin 30 % hamppukuituja ja loput 70% epoksimatriisia. Levyistä valmistettiin vesileikkurilla vetosauvoja, joiden mekaaniset ominaisuudet testattiin Instron 8874 –vetotestauslaitteella.


Keskeisiä tuloksia
Oheisessa taulukossa on mekaanisen testauksen tuloksia kuitukimpuille. Mekaanisesti käsitellyt kuidut olivat lujimpia ja jäykimpiä.

Mekaanisesti prosessoitujen kuitujen paremmuus näkyi vastaavasti myös niistä valmistetuissa komposiiteissa ja vetosauvojen testauksessa eli niistä saatiin lujimmat ja jäykimmät komposiitit. Kuitujen erilaiset käsittelyt vaikuttivat merkittävästi myös komposiittien kosteuden imeytymiseen.
Optinen mikroskopia
Optinen mikroskopia on menetelmä, jossa näyte valaistaan ja sitä tarkastellaan suurennettuna linssien läpi. Valaisu voidaan tehdä ala- tai yläpuolelta riippuen näytteen valonläpäisykyvystä.
Laitteisto
- Valomikroskooppi Carl Zeiss AxioImager M2+ värikamera Axiocam MRc
- 1.25x, 2.5x, 5x, 10x, 20x, 40x, 50x and 100x objektiivit
- Fluoresenssivarustus (UV, FITC, GFP ja Rhodamine)
- Pintavalovarustus heijastaville näytteille
- Polarisaatiovarustus
- Motorisoitu näytepöytä mahdollistaa esim. suurten näytteiden kuvauksen (”mosaiikkikuvaus”) tai heijastavien näytteiden pinnankarheuden määrittämisen.
- Valomikroskooppi Nikon Microphot FXA + Hamamatsu ORCA b/w-kamera
- Mm. DIC- ja faasikontrastioptiikalla varustettu laitteisto. Optimoitu tällä hetkellä densitometria-käyttöön.
- Käänteismikroskooppi Nikon TE-300
- Laboratoriomikroskooppi Zeiss Primo Star + AxioCam ERc 5s värikamera
- Objektiivit 4x, 10x, 40x ja 100x (oil)
- Stereomikroskooppeja
- Carl Zeiss, Leica; pintojen tarkasteluun suuristakin näytteistä
- Leica MZ75 + digitaalikamera Nikon DS-Fi2 ja ohjausyksikkö DS-L3
- Zeiss Stemi DV4
- Leica EZ4; sisäänrakennettu värikamera
- Pintaplasmoniresonanssi-spektrometri Biacore X; biomolekyylien sitoutumisen tutkintaan
Näytevaatimukset
Pin-on-disk -kitka/kulumisanalyysi
Pin-on-disk-testissä näytteen pintaa painetaan kuormitetulla tapilla ja näytettä pyöritetään samanaikaisesti, jolloin pinnalle muodostuu ympyrämäinen kulumisura. Tapin päässä voidaan käyttää myös erillistä metallista tai keraamista kuulaa. Tappiin kohdistuvan sivuttaisvoiman mittauksella saadaan selville kitkavoima ja tapin/kuulan sekä näytteen muodostaman materiaaliparin kitkakerroin. Näyte voidaan myös upottaa testin ajaksi nesteeseen, jolloin saadaan selville voitelun vaikutus sen kitkaominaisuuksiin. Kulumisen voimakkuutta voidaan säädellä muuttamalla tapin/kuulan kuormitusta, näytteen pyörimisnopeutta tai testin kestoa. Lisäksi lämpötila ja ilmankosteus vaikuttavat tyypillisesti tuloksiin. Kitkavoiman äkillisiä muutoksia tarkastelemalla voidaan esim. tutkia pinnoitteen puhki kulumista. Kulumisuraa voidaan tarkastella jälkikäteen esim. optisella mikroskoopilla tai pyyhkäisyelektronimikroskoopilla.
Laitteisto
- kaksi omavalmisteista pin-on-disk-tribometriä
- toinen tasaisille näytteille ja toinen tasaisille/sylinterimäisille näytteille
- standardi ASTM G99
Näytevaatimukset
- näytteen maksimikoko tarkasteltava tapauskohtaisesti, pyörimisliikkeen takia näyte ei voi olla kovin suuri tai painava
- testattava näyte tasainen tai sylinterimäinen
- näytteen minimihalkaisija vaakasuunnassa n. 30 mm
Pinnoitettujen teräskappaleiden korroosiopotentiaalin määritys
Tutkimuksessa selvitettiin kahden erilaisen jälkikäsittelyn vaikutusta kromipinnoitettujen teräskappaleiden korroosio-ominaisuuksiin mittaamalla kappaleiden korroosiopotentiaalit ja –virrantiheydet suolaliuoksessa. Korroosiopotentiaali on yhteydessä näytteen korroosioalttiuteen ja korroosiovirrantiheys korroosion etenemisnopeuteen. Kolmesta tutkitusta näytteestä yksi oli käsittelemätön referenssinäyte ja kahdelle muulle suoritettiin hieman toisistaan poikkeava jälkikäsittely, jolla pyrittiin parantamaan pinnoitteiden korroosiosuojaa.
Mittaukset suoritettiin Solartron 1287 –potentiostaatilla potentiodynaamisena polarisaatiomittauksena 3-elektrodikytkentää käyttäen. Tulokset kerättiin Corrware-ohjelmalla ja näytteiden korroosiopotentiaalit sekä –virrantiheydet määritettiin saaduista polarisaatiokäyristä graafisesti Tafelin menetelmällä.

Kuva 1: Polarisaatiokäyrät

Lopputulokset
Jälkikäsiteltyjen näytteiden korroosiopotentiaalit ja -virrantiheydet olivat itseisarvoltaan pienempiä kuin referenssinäytteellä, joten ne olivat vähemmän alttiita korroosiolle ja korroosioreaktiot tapahtuivat niissä hitaammin. Pinnoitteen jälkikäsittelyillä saavutettiin siis haluttu korroosio-ominaisuuksia parantava vaikutus käsittelemättömään näytteeseen verrattuna. Kahdesta jälkikäsittelymenetelmästä jälkimmäinen paransi korroosio-ominaisuuksia hieman enemmän kuin ensimmäinen.
Pyyhkäisyelektronimikroskopia (SEM-EDS)
Carl Zeiss HD/VP on korkean resoluution pyyhkäisyelektronimikroskooppi, jolla voidaan kuvata sekä sähköä johtavia, että johtamattomia näytteitä. EDS mahdollistaa näytteiden alkuainekoostumuksen selvittämisen. Laitteella voidaan kuvata näytteiden morfologiaa mikro- tai nanomittakaavassa. Lisäksi esimerkiksi pinnoitteista voidaan tehdä 3D -malli laitteen ohjelmistolla.
Laitteisto
- HR-SEM: Carl Zeiss, Sigma HD/VP
- Suurennuskyky 20 – 50 000x
- Erotuskyky jopa 1.0 nm
- Huonosti sähköä johtavien tai pölymäisten näytteiden pinnoitus kullalla, kromilla tai hiilellä
- Variable Pressure – moodi kosteiden tai sähköä johtamattomien näytteiden tarkasteluun
- High Vacuum – moodi sähköä johtavien kuivien näytteiden tarkasteluun
- Kaksi Thermo Noran 60 mm2 EDS-detektoria
- Näytteen alkuainekoostumus massa- ja atomi-jakauman mukaan
- Koostumus-mittaus voidaan tehdä isommasta alueesta tai yksittäisestä pisteestä.
- Pinnan rakenteiden 3D -mallinnusohjelmisto
- Pinnan karheuden määritys laskennallisesti
Näytevaatimukset
- esimerkiksi jauhemaisia, ohut kalvoja, biologisia tai epäorgaanisia.
- Monipuolisia näytteenpitimiä erityyppisille näytteille (max. 65 x 65 mm)
Raman-mikrospektroskopia
Raman-spektrometrilla kuvannetaan materiaalin kemiallista rakennetta ja koostumusta laservalon avulla. Raman-spektroskopiassa näyte viritetään laserilla virtuaaliselle värähdystilalle ja viritystilan purkautuessa Raman-siroava säteily mitataan. Tuloksena saadaan spektri, jossa sironnan intensiteetti esitetään aallonpituuden muutoksen funktiona. Ramanilla voidaan tutkia materiaalin sisältämiä vyöhykkeitä tarkasti, sillä laservaloa ohjataan mikroskoopilla. Menetelmä soveltuu orgaanisten aineiden tunnistamisen lisäksi myös epäorgaanisten komponenttien tunnistamiseen, esim. mineraalit, metallioksidit.
Laitteisto
- Thermo DXR2xi; kuvantava Raman-mikrospektrometri
- Käytössä kaksi eri laser-aallonpituutta (532 nm ja 785 nm) eri näytetyypeille.
- Spektrialue 3800 – 50 cm-1
- 10x, 20x, 50x, 100x ja vesi-immersio-objektiivit
- Erotuskyky n. 1 µm
- Konfokaalisen mittausmoodin avulla voidaan tutkia esim. kerrosrakenteiden koostumusta näytettä rikkomatta.
- Näytteiden kemiallisen koostumuksen määritys joko pistemittauksena tai kartoittamalla ainesosien jakaumia.
- Lämpöpöytä, jonka avulla voidaan tutkia näytteen kemiallisen koostumuksen muutosta lämpötilan vaikutuksesta
- Data analyysi Thermo OMNIC tai MATLAB
- Laaja spektrikirjasto näytteiden tunnistamisen avuksi
Näytevaatimukset
- Ei voimakkaasti fluoresoivia
- Näytteen maksimikoko n. 15 x 10 x 4 cm
- Pienempi näyte helpompi käsitellä
Röntgenfotoelektronispektroskopia (XPS/ESCA)
XPS, eli röntgenfotoelektronispektroskopia (X-ray photoelectron spectroscopy) on pintaherkkä menetelmä alkuaineiden ja kemiallisten sidosten määritykseen. XPS on ainetta rikkomaton mittausmenetelmä, jonka avulla voidaan analysoida kaikkia heliumia raskaampia alkuaineita. Tulokset saadaan semikvantitatiivisesti joko paino- tai atomiprosenttiosuuksina. Alkuaineet on myös mahdollista kartoittaa 2D-kuvaan kappaleen pinnasta. XPS kulkee toisinaan myös nimellä ESCA (Electron Microscopy for Chemical Analysis), kyseessä on siis tismalleen sama menetelmä.
Analyysit
- Erittäin pintaherkkä menetelmä. Menetelmävalinnan mukaan analyysisyvyys aivan ylimmästä atomikerroksesta 10 nm:iin
- Semikvantitatiivinen alkuaineanalyysi ainetta rikkomattomalla menetelmällä
- Alkuaineiden hapettumistilat, jotka myös mahdollista kvantifioida
- Alkuaineiden 2D-kuvantaminen, resoluutio parhaimmillaan 10 μm
- Syvyysprofilointi kaikenlaisille materiaaleille. Klusteritykki mahdollistaa myös herkkien polymeerinäytteiden syvyysprofiloinnin
- Valenssienergioiden ja työfunktion määrittäminen UPS:llä
- Band gap-määritys REELS:llä
- Alkuaineiden tunnistus ylimmältä atomikerrokselta ISS:llä
Laitteisto
- Thermo Fisher Nexsa G2, moderni XPS-laitteisto, jossa energiaresoluutio jopa < 0.5 eV FWHM
- Argon klusteritykki pintakerrosten sputterointiin, jossa sekä monatominen että klusterimoodit mahdollisia (MAGSIS)
- 2D-kuvantaminen, spatiaaliresoluutio jopa 10 μm
- Sekä positiivinen että negatiivinen varauskompensaatio eri mittausmoodeille ja eristävien näytteiden tarkkaan analyysiin
- Mittaukset tyhjiössä, paine 5xE-9 mbar
Lisämenetelmät
- UV fotoelektornispektroskopia (UPS)
- Ionisirontaspektroskopia (ISS)
- Heijastuneiden elektronien energiahäviöspektroskopia (REELS)
- Lämpölevy näytteiden kuumentamiseen mittauksen yhteydessä, lämpötila max. 800 deg C
- Ilmalle sensitiivisten näytteiden valmistus Ar-hanskakaapissa ja siirtomoduuli laitteen näytesyöttöön
Näytevaatimukset
- Näytedimensiot max 60 mm x 60 mm x 20 mm (pituus x leveys x korkeus)
- Vain kiinteässä olomuodossa oleville näytteille tyhjiön takia
Röntgentomografia MikroCT
Röntgentomografialla voidaan määrittää kappaleen sisärakenne näytettä rikkomatta mikrometriluokan tarkkuudella. Yleisesti ottaen mitä pienempi näytekappale sen tarkemmin se voidaan kuvata. Halkaisijaltaan alle 3 mm näytteestä voidaan nähdä jopa 1 mikrometrin kokoisia yksityiskohtia. Koripallon kokoiselle näytteelle kuvapikselin koko on 100 mikrometriä. Laitteella saadaan sekä röntgenkuvia halutusta suunnasta että tomografiakuvasarjoja. Leikekuvasarja voidaan suunnata ja analysoida tarpeen mukaan. Kuvista voi esimerkiksi arvioida materiaalin homogeenisuutta, rakennevirheitä, huokosia ja vieraskappaleita tai kuitujen suuntautumista.
Laitteistot
- Skyscan 1172 soveltuu pienten, parin senttimetrin kokoisten metallittomien näytteiden kuvantamiseen.
- Nikon XTH 225 soveltuu halkaisijaltaan alle 25 cm kokoisten näytteiden sekä pienten metallinäytteiden kuvantamiseen. Läpäisykyky on noin 3 cm terästä tai 12 cm alumiinia.
- Visualisointi- ja analysointiohjelmistoina mm. Volume Graphics Studio Max ja Bruker CT Analyser
- Röntgen- tai leikekuvasarjoista voidaan tehdä video
- Eri tavoin rajatut osat voidaan näyttää eri väreillä
- Kohteen piirteitä voidaan korostaa väärävärikuvassa
- Leikekuvista voidaan muodostaa 3D-kuvia ja stl-tiedostoja
- 3D-kuvista voidaan tehdä video
Näytevaatimuksia
- Kuvantamisen tarkoitus on selkeä
- Kiinnitettävissä liikkumattomaksi
- Kuvausalalle sopiva kappale
- Riittävästi röntgensäteilyä läpäisevä kappale
- Vähäinen lämpöliikunta kuvauksen aikana
- Turvallisesti käsiteltävissä
Termogravimetria TGA
Menetelmällä mitataan näytteen massan muutosta lämpötilan funktiona. Lämpötilan noustessa tapahtuu näytteessä kemiallisia (kemisorptio, hajoaminen ja oksidoituminen) ja fysikaalisia muutoksia (faasimuutokset, adsorptio ja desorptio) joilla on vaikutusta näytteen massaan. Mittaukset voidaan suorittaa joko synteettisessä ilmassa, tai inertissä typpiatmosfäärissä eri ilmiöiden tutkimiseksi. Menetelmällä voidaan tutkia esimerkiksi näytteen kosteuspitoisuutta, haihtuvien yhdisteiden määrää tai termistä stabiilisuutta. Mitatusta signaalista saadaan derivoimalla myös DTA-käyrä (Differential thermal analysis), joka mahdollistaa toisiaan lähellä olevissa lämpötiloissa tapahtuvien ilmiöiden erottelun.
Laitteisto
- NETZSCH: TG 209 F1 Libra
- Automaattinen näytteenvaihtaja jopa 192:lle näytteelle.
- Mittaukset voidaan suorittaa synteettisessä ilmassa tai typpikaasussa
- Lämpötilaväli: Huoneenlämpö -> 1100 °C
- Lämmitysnopeus max. 200 °C/min
- Vaa’an tarkkuus 0.1 µg
Näytevaatimukset
- Näytemäärä tyypillisesti 2-50 mg. Vähintään 1 mg suositeltavaa, ja maksimimäärä 1 g.
- 50 µl näytekuppi
Vetokoe
Vetokokeen avulla voidaan määrittää materiaalin lujuusominaisuuksia ja käyttäytymistä kuormituksen alaisena. Vetokokeessa testikappaletta vedetään kasvavalla voimalla, kunnes kappale katkeaa. Kappaleeseen kohdistuneesta voimasta saadaan käyrä josta voidaan laskea materiaalin ominaisuuksia kuten vetolujuus, murtolujuus ja plastisuus. Tietoa materiaaliominaisuuksista tarvitaan eri käyttösovellutusten määrittelyssä ja laadunvalvonnassa. Vetokoetta voidaan myös käyttää esim. hitsin tai kokonaisen rakenteen lujuuden tutkimiseen.
Laitteisto
- Vetokoetta varten koneistetaan vetosauvat, tai vetokoe voidaan suorittaa myös kokonaiselle tuotteelle, jolloin saadaan testattua rakenteesta esim. hitsiliitoksen lujuus.
- Staattisena vetokokeena 1 kN – 500 kN
- Dynaamisena vetokokeena 2,5 kN – 500 kN
- Olosuhdekammion avulla kylmä ja kuuma testaus.
- Standardi: SFS – EN ISO 6892–1:2016
Näytevaatimukset
Kobolttijauheiden faasikoostumuksen määritys röntgendiffraktiolla
Case-tapaus: Kobolttijauheiden faasikoostumuksen määritys röntgendiffraktiolla
Tutkimuksen kohteena oli 3 erilaista kobolttihienopulverinäytettä. Kaikki näytteet olivat puhdasta kobolttia, ja niistä
oli tarkoitus selvittää koboltin eri faasien suhteelliset osuudet. Näytteiden sisältämät koboltin faasit tunnistettiin
röntgendiffraktiolla, ja niiden suhteelliset osuudet määritettiin laskennallisesti Rietveld-hienonnuksella.
Mittaukset suoritettiin Bruker D8 DISCOVER diffraktiolaitteistolla ja mittauksissa käytettiin Mo Kα-säteilylähdettä.
Mittauksista saaduista diffraktogrammeista tunnistettiin näytteissä esiintyvät koboltin faasit DIFFRAC.EVA 3.1-ohjelmistolla
hyödyntäen PDF-2 2015 tietokantaa. Rietveld-hienonnus suoritettiin käyttämällä TOPAS 4.2-ohjelmistoa.

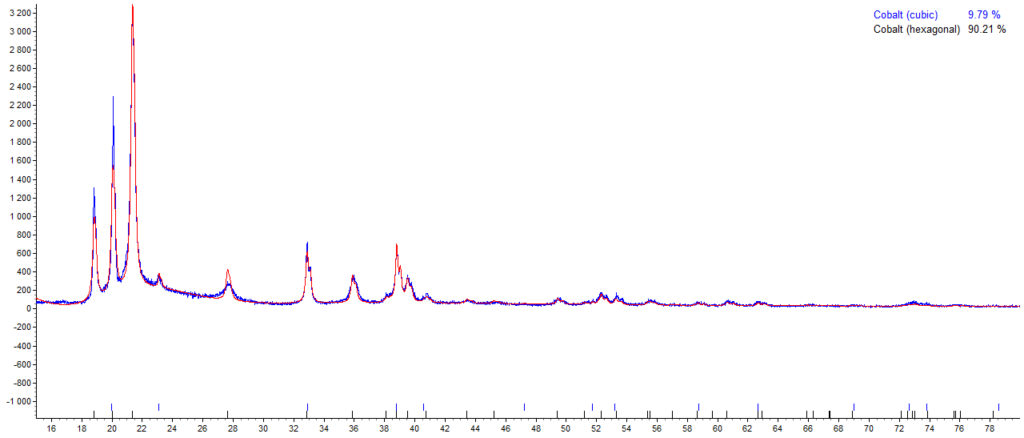
Taulukko 1: Koboltin faasien suhteelliset osuudet
Näyte | Kuutiollinen [%] | Heksagonaalinen [%] |
Ajo 10 | 9,8 | 90,2 |
Ajo 16 | 14,0 | 86,0 |
Ajo 21 | 8,7 | 91,3 |
Lopputulokset
Näytteissä havaittiin kahta kiteistä koboltin faasia: kuutiollista ja heksagonaalista. Faasien suhteelliset massa-
osuudet olivat kaikissa näytteissä samaa kokoluokkaa: noin 1:9. Tulosten perusteella näytteessä Ajo 16 olisi muita
näytteitä enemmän kuutiollista faasia, kun taas näytteet Ajo 10 ja Ajo 21 olivat koostumukseltaan lähes samoja.
Lisäksi tuloksista oli havaittavissa, että faasien välillä oli myös morfologisia eroja. Kuutiollisen faasin diffraktiopiikit
olivat kaikki yhtä leveitä, kun taas heksagonaalisella faasilla diffraktiopiikkien leveydet vaihtelivat piikkikohtaisesti.
Tämä viittaisi siihen, että kuutiollisen faasin kiteet ovat pyöreitä, kun taas heksagonaaliset kiteet suosivat tiettyjä kasvusuuntia.
Syy tähän voi löytyä valmistusprosessista.
Asbestikuitujen identifiointi standardikuituja hyödyntäen
Case-tapaus: Kuitujen kirjastointi SEM EDS-laitteistolla asbestistandardi- ja mineraalikuituja hyödyntäen
Tutkimuksessa hyödynnettiin laboratoriossamme aiemmin tutkittuja olemassa olevia tunnettuja kuitumateriaaleja sekä amerikkalaiselta tukkurilta hankittuja erittäin puhtaita asbestikuitustandardeja. Kuidut pinnoitettiin SEM:ia varten Au-pinnoitetteella ja kuvattiin SEM-laitteella analysoiden ne EDS-analysaattorilla käyttäen kolmea eri elektronisuihkun kiihdytysjännitteen energiaa. Lisäksi testi toistettiin pinnoittamattomilla näytteillä käyttäen matalapaineista (20 Pa) typpikaasua näytekammiossa.
Tulokset ovat nyt hyödynnettävissä, ja kuitutyypit voidaan tunnistaa ja lähes kaikki asbestikuidut voidaan identifioida. Lisäksi myös muista mineraalikuiduista saadaan tunnistettua rakennusmateriaaleina yleisesti käytettävät kuidut.
Kuvaukset suoritettiin Zeiss SigmaHD|VP pyyhkäisyelektronimikroskoopilla ja analyyttiset mittaukset tehtiin Thermo Noran-järjestelmällä. Mitatut Röntgenspektrit tunnistettiin ja kirjastoitiin omaan kuitutietokantaan Thermo Pathfinder-ohjelmistoon.
Mikrorakennetutkimus
Materiaalien mikrorakennetutkimuksessa käytetään mikroskooppeja, joiden avulla voidaan analysoida metallien kiderakennetta. Samalla menetelmällä voidaan havaita metallien ja/tai hitsien sulkeumat, erkaumat, rakenneviat sekä pinnoitteet. Mikrorakennetutkimuksen avulla voidaan tarkastella eri lämpökäsittelyiden vaikutusta kiderakenteeseen sekä arvioida raekokoa. Nämä kaikki vaikuttavat tutkittavan materiaalin ominaisuuksiin ja saattaa paljastaa hitsausvirheitä, joita ei visuaalisesti ilman mikroskopiaa olisi voitu havaita.
Mikrorakennetutkimuksessa näytteestä valmistetaan hie, jota tutkimalla voidaan selvittää vaurioanalyysissä esimerkiksi vaurion perinnäinen syy. Näitä syitä voi olla esimerkiksi ei-toivottu hitsin karkeneminen, karkearakeisen raekoon muodostuminen liiallisesta lämmöntuonnista johtuen hitsauksessa, ei-toivottujen faasien muodostuminen hitsauksen yhteydessä tai pallografiittivalujen grafiitin epätäydellinen palloutuminen valuissa.
Kiderakenteen tekstuuri
Kiteisen aineen tekstuurilla tarkoitetaan sen kiteiden orientaatioiden jakaumaa. Materiaalilla ei ole kristallografisessa mielessä tekstuuria, jos sen kiteet ovat täysin satunnaisesti orientoituneita. Kuitenkin usein esimerkiksi metallien kiteet järjestäytyvät systemaattisesti tiettyihin orientaatiohin työstön seurauksena. Tekstuurin johdosta materiaalin mekaaniset ominaisuudet voivat muuttua tarkastelusuunnasta riippuen (ns. anisotrooppinen materiaali). Esimerkiksi metallia taivuttamalla voidaan luoda erittäin teksturoitunut rakenne taitoskohtaan.
Materiaalin tekstuuri voidaan määrittää röntgendiffraktion avulla. Tekstuurimittauksessa kappaletta kierretään kahden kiertokulman suuntaan ja tarkastellaan diffraktiopiikkien intensiteettimuutoksia kiertokulmien funktiona. Näin saaduista 2D-kuvaajista käytetään nimitystä poolikuvaaja (engl. Pole figure), ja niiden avulla voidaan rekonstruoida 3D-jakauma koko materiaalin tekstuurista. Erilaiset tekstuurit synnyttävät erilaiset poolikuvaajat. Alla esitetty esimerkki kuitumaisen tekstuurin synnyttämästä poolikuvaajasta.

Fysikokemiallinen karakterisointi
Nanomateriaalien fysikokemiallinen karakterisointi on laaja tutkimusalue ja kattaa useita eri tutkimusmenetelmiä. Tyypillisimpiä tutkimuksen kohteita ovat materiaalin koko, muoto, pintaominaisuudet, kemiallinen koostumus, mahdolliset epäpuhtaudet sekä stabiilisuus. MATERIA tutkimuskeskuksella on käytössään erinomainen varustelu nanomateriaalien laajaan tutkimukseen.
MATERIA tutkimuskeskuksen menetelmät fysikokemialliseen karakterisointiin
Kaasuadsorptio huokoisten materiaalien huokoskokojakauman ja ominaispinta-alan määritykseen
Elektronimikroskopia (SEM & TEM), varustettuna EDS alkuaineanalyysillä
Dynaaminen valonsironta partikkelikoon ja Zeta-potentiaalin määritykseen
Spektroskooppiset menetelmät (FTIR & Raman) molekyylirakenteen analysointiin
Röntgendiffraktio (XRD) kiderakenteen ja -koon määritykseen
Termiset menetelmät (DSC & TGA) termodynaamisiin analyyseihin
Matalan tulokulman diffraktio
Matalan tulokulman diffraktio (engl. Grazing Incidence Diffraction, GID) on röntgendiffraktioon pohjautuva menetelmä materiaalien pintakerrosten tutkimiseksi. Nimensä mukaisesti menetelmässä kohdistetaan näytteeseen röntgensäteitä matalalla tulokulmalla, jolloin absorption johdosta mitattu diffraktiosignaali syntyy vain pintakerroksesta. Kasvattamalla tulokulmaa saadaan röntgensäteet tunkeutumaan syvemmälle näytteeseen, ja näin ollen voidaan määrittää faasien jakautumista syvyyden funktiona. Syvyysprofiilin määritys on erityisen kiinnostava esimerkiksi pinnoitteille, joiden epäillään muodostavan diffuusiokerroksia substraatin rajapintaan.
Lue lisää röntgendiffraktiosta täältä.
Röntgenreflektometria
Röntgenreflektometria on ohuiden pinnoitteiden analysointiin käytettävä menetelmä, jolla saadaan tietoa pinnoitteen karheudesta, paksuudesta, sekä pinnoitekerrosten tiheydestä. Menetelmässä pinnoitteeseen kohdistetaan röntgensäteitä matalalla tulokulmalla, jotka heijastuvat eri rajapinnoista muodostaen diffraktiokuvion (ns. Fringe-kuvio). Mitatusta Fringe-kuviosta voidaan laskea pinnoitteen karheus, paksuus, ja röntgensäteiden absorptioon liittyvä tiheys. Vastaava Fringe-ilmiö on havaittavissa näkyvän valon tapauksessa esimerkiksi veden päällä olevassa öljykerroksessa kun valo heijastuu öljy-vesi rajapinnasta muodostaen silminnähtäviä värikkäitä kuvioita.
Menetelmä vaatii erittäin sileän ja ohuen pinnoitteen toimiakseen. Pinnasta on kyettävä näkemään oma peilikuvansa ja pinnoitepaksuus voi olla maksimissaan ~200 nm. Pinnoite voi koostua myös useasta ohuemmasta pinnoitekerroksesta, jolloin tietoa on mahdollista saada myös pinnoitekerrosten rajapintojen karheudesta. Kuitenkin kerrosten määrän kasvaessa menetelmän tarkkuus heikkenee.
